sheet metal stamping design PRODUCT DESIGN FOR SHEET METAL STAMPING - 16 HOURS. This advanced practical course is a tool-maker and stamper's perspective of product design. The goal of this course is to highlight the "true cost" of part features . Explore a wide range of our Water Meter Boxes selection. Find top brands, .
0 · wholesale custom sheet metal stamping
1 · sheet metal stamping near me
2 · sheet metal stamping design guidelines
3 · sheet metal stamping basics
4 · sheet metal stamping at home
5 · metal stamping service near me
6 · metal stamping process flow chart
7 · automotive sheet metal stamping process
sheet metal workers union local no. 10 wage sheet effective may 1, 2024 through april 30, 2025 page 1 of 1
This comprehensive guide is designed to equip engineers and designers with the knowledge and insights to optimize their sheet metal stamping designs. From material . The following are some design rules for slots and holes. Hole and slot in sheet metal design. 1. The minimum hole diameter should be ( Dmin) ≥ the thickness of the sheet .
Stamping Basics Involve us during design stage to optimize cost and performance in component design. Engineering changes can be costly. While stamping offers precision and good . Master sheet metal stamping design with this comprehensive guide. Learn essential tips on material selection, bend design, and tooling for optimal results.
PRODUCT DESIGN FOR SHEET METAL STAMPING - 16 HOURS. This advanced practical course is a tool-maker and stamper's perspective of product design. The goal of this course is to highlight the "true cost" of part features .!“Design for Sheetmetal Working”, Ch. 9 Boothroyd, Dewhurst and Knight . Examples-sheet metal formed . Female die Male die (punch/post) Metal sheet Blank holder (ring) on cushion Compressible cushion Sheet metal stamping/drawing – car industry •90million cars and commercial vehicles produced worldwide in 2014 . Stamping Auto body panels .Die Tooling Preventive Maintenance for the Sheet Metal Stamping Industry: A Comprehensive, Step-by-Step Guide to Control Your Sheet Metal Stamping Process Thomas J. Ulrich 4.2 out of 5 stars 5Sheet Metal Stamping Dies Die Design and Die-Making Practice. by Vukota Boljanovic. 224 Pages, 6.00 x 9.00 x 0.60 in. Paperback; ISBN: 9780831134631; Availability: Print On Demand; Publication Date: July 2012; .95. BUY EDUCATORS: REQUEST AN EBOOK REVIEW COPY. Description ; About the Author;
Key Considerations for Sheet Metal Stamping Design: To ensure your sheet metal stamping project is successful, it’s essential to consider several critical design factors that can significantly impact the manufacturing process and the final part’s quality. Let’s explore these key considerations: 1. Material Selection . The choice of .
Vukota Boljanovic, Ph.D., has nearly 50 years of experience in applied engineering in the aircraft and automotive industries, as well as academia.He has performed extensive research in manufacturing engineering, including the impact of design and modification on sheet metal dies, jigs and fixtures, and process selection, aircraft assembly, and inspection tool and .
Read on to unlock the secrets of sheet metal stamping. 1. Step#1 Design and Planning Stage. To begin the sheet metal stamping journey, a careful design and planning set the stage for success. Here are the crucial steps involved in this initial phase: Understanding Client Requirements: The process starts by thoroughly understanding the client . Sheet Metal Stamping is a low-cost high-speed manufacturing process that produces a high volume of identical metal components, which has contributed importan. Sheet metal stamping is a versatile and efficient manufacturing process capable of producing a wide array of complex parts for various industries. However, designing parts for sheet metal stamping requires a specialized understanding of engineering principles and manufacturing limitations.. This comprehensive guide is designed to equip engineers and designers with the . How is the K-Factor important in sheet metal design? The K-Factor in sheet metal design is a ratio that represents the location of the neutral axis with respect to the thickness of the sheet metal. An accurate K-Factor is crucial for predicting the amount of stretch or compression of the material during bending, ensuring accurate part creation.
Design of sheet metal forming tooling is currently based on that experienced tooling designers with good knowledge of how stamping tools previously have been designed and operated in production .Progressive Die Design is our SPECIALTY, but we do design all types of Sheet Metal Stamping dies. We use ICEM DDN for 2-D Design and Vero International for 3-D Design . Using VISI, our 3-D Design Software, we are capable of computing a flat blank from a complex 3-D model to help with stock utilization.The sheet-metal stamping process is modeled in a manner suitable for multiple-input multiple-output control system design, with commercially available sensors and actuators. . Process Control for Sheet-Metal Stamping allows the reader to design and implement process controllers in a typical manufacturing environment by retrofitting standard . Sheet Metal Stamping Analysis and Process Design based on the Inverse Approach Jean‐Louis Batoz; Jean‐Louis Batoz 1 Université de . be presented to show the actual capabilities of the coupled analysis and optimization strategy with application to the design of stamping parameters. Topics. Optimization algorithms. This content is only .
Stamping Design Manual Collaborative product - process development guidelines for high strength steel stampings. A . or for mass reduction through a reduction in sheet metal thickness, or gauge. An increase in strength generally leads to reduced ductility or formability. Care must be taken in designing parts, tooling, and fabrication .Metal Stamping Design Guidelines Metal Stamping is an economical way of producing quantities of parts that can have many qualities including strength, durability; wear resistance, good conductive . There are many sheet and strip materials to choose from that respond well to metal stamping and forming. However, price and availability can vary .For Sheet Metal Stamping Process . 4 Process Control For Sheet Metal Stamping Process Modeling Controller Design And Shop Floor Implementation Advances In Industrial Control 2020-06-17 shown in Fig. 1.Developmen t of process control in

A stamping die is a special, one-of-a-kind precision tool that cuts and forms sheet metal into a desired shape or profile. . Art also has written technical articles on stamping die design and build for a number of trade publications. A recipient of many training awards, he is active in metal stamping training and consulting worldwide. .The document describes the design of an automatic sheet metal stamping machine. The machine was designed to solve productivity problems at a steel product company by providing an easier and more efficient stamping process compared to traditional manual methods. The design process involved collecting data from the company, researching existing stamping machines, .Stamping dies are the tools that shape and cut sheet metal parts. They are commonly developed using computer-aided design (CAD) software and analytical programs to create and prove-out highly accurate, unambiguous designs. These designs are then translated into stamping dies by skilled craftsmen, known as diemakers. Once these stamping dies are mounted into presses, .
Sheet Metal Process - Stamping. . Corner fillets are employed in sheet metal design to transform sharp edges into rounded ones, mitigating safety hazards and ensuring that the part is easily removed from the tool. These rounded edges not only enhance safety but also facilitate ease during assembly, surface treatment, and packaging processes. . A stamping die is a special, one-of-a-kind precision tool that cuts and forms sheet metal into a desired shape or profile as the sheet metal is pressed, or stamped, between two mating components. A die gets the force it needs from a press. The part produced by stamping the sheet metal between the dies in the press is called the piece part.
wholesale custom sheet metal stamping
sheet metal stamping near me
To help fine tune the stamping process and finalize die design, die makers use an analytical tool called Circle Grid Analysis, or CGA. The application of CGA involves the . Most sheet metal stamping uses materials: a. .020” to .080” thick b. .050” to .125” thick c. .001” to 1.000” thick d. .010” to .060” thick
Sheet metal Stamping design with Fusion 360 - Chassis frame. Learn how to design the chassis frame from scratch with methodology and CAD workflows for mechanical engineers. Rating: 4.4 out of 5 4.4 (41 ratings) . A deep dive into the world .Find many great new & used options and get the best deals for Sheet Metal Stamping Dies : Die Design and Die-Making Practice by Vukota Boljanovic (2012, Trade Paperback) at the best online prices at eBay! Free shipping for many products!
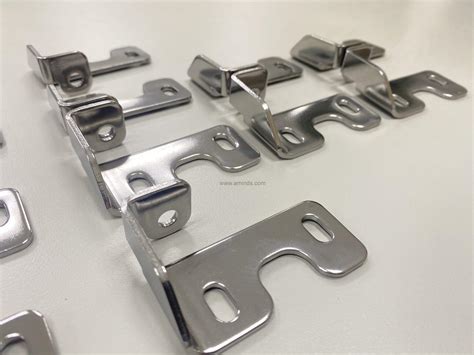
sheet metal stamping design guidelines
Progressive die stamping for sheet metal fabrication is a complex process. For that reason, you want to design the tooling accurately in order to achieve the quality part you want. . Sheet Metal Design Guidelines: Designing Sheet Metal Parts. 11/1/2023. Design for Manufacturability. Preparing Technical Drawings for Your Sheet Metal Fabricator .
sheet metal stamping basics
We follow Sheet metal design guidelines to ensure the quality and manufacturability of sheet metal enclosures. As a result, you can deliver the product at a low cost and faster timeline. It is difficult to follow all sheet metal design guidelines for complex sheet metal parts. Therefore exceptions can be there for complex sheet metal parts.
sheet metal stamping at home

Building a warehouse home from the ground up also has durability benefits, however, since most warehouse homes are made of steel. Reclaimed materials. When converting a warehouse into a residence, there should be materials that are part of the original site that can be reclaimed and upcycled in the new design.
sheet metal stamping design|metal stamping process flow chart