chassis metal matrix composites Automotive chassis is used for supporting the functioning structure and balancing on the road. Being an initial requirement chassis vehicles like trucks, trailers, and semi-trailers .
$9.99
0 · Weight Optimization of Chassis of an Automotive Vehicle
1 · Weight Optimization of Chassis of an Automotive
2 · Structural analysis and weight optimization of automotive chassis
3 · Structural analysis and weight optimization of
4 · Metal
5 · Material Optimization of Chassis using Metal Matrix Composites
6 · Heterostructured metal matrix composites for structural
7 · Automotive chassis components lighten up with composites
8 · A review on aluminum matrix composites' characteristics and
Ignition off, pull the HVAC/ECAS fuse for 10 seconds, reinstall and start vehicle without touching any controls, wait 40 seconds for the control module to self calibrate. If there is still a problem, the actuator for the temp blend door may have failed.Several Journeymen have stated that if you run metal conduit, the conduit is considered grounded, thus a ground screw in every j-box is not required (the same answer applies if you're running MC cable). However, 1 guy (the one who I first started with says they .
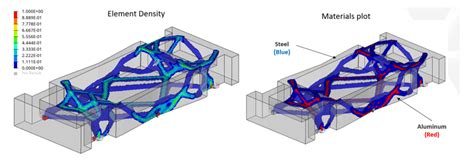
Metal-matrix composites offer considerable promise to help automotive engineers meet the challenges of current and future demands for recyclable, fuel-efficient, safe, and low-emission . Composite and hybrid components reduce mass, increase functionality on electric and conventional passenger vehicles. As automakers seek to reduce the curb weight of . Aluminum matrix composites (AMCs), known for their lightweight, high strength, and excellent corrosion resistance, have demonstrated substantial potential in vehicle . The presented work focuses on optimizing a heavy-duty TATA 1612 truck chassis (ladder type frame) by substituting its material from conventional steel with potential metal matrix composite.
Heterogeneity design is a promising strategy to solve the strength-ductility/toughness tradeoff in metal matrix composites (MMCs) via maximizing the intrinsic .

Automotive chassis is used for supporting the functioning structure and balancing on the road. Being an initial requirement chassis vehicles like trucks, trailers, and semi-trailers .The current chassis mass with traditional material is 1560 Kg which is made up of structural steel, whereas the chassis mass with Aluminium carbide metal matrix composite material is 523.45 Kg.
Abstract: With increase in fuel prices and demand for lightweight materials in manufacturing of Heavy Motor Vehicle (HMV) chassis is high, the current research envisaged the application of . For this we have taken three materials like structural steel, carbon fiber and Aluminium silicon carbide metal matrix composite. The automotive chassis is the vehicle's base, providing. Results shows that, the mass of chassis is 62.564Kg and 71.502 Kg using Graphite Al GA 7-230 and Al6092/SiC/17.5p MMC respectively whereas the actual mass is 214 Kg in case of conventionally used Structural steel alloy. Therefore, a significant amount of mass is reduced considering a number of other performance factors. 1. Introduction.Metal-matrix composites offer considerable promise to help automotive engineers meet the challenges of current and future demands for recyclable, fuel-efficient, safe, and low-emission vehicles. These materials can be engineered to match the design requirements of automotive power-train or chassis components.
Weight Optimization of Chassis of an Automotive Vehicle
Composite and hybrid components reduce mass, increase functionality on electric and conventional passenger vehicles. As automakers seek to reduce the curb weight of conventional and electric vehicles (EVs), metal chassis components have become a significant target for conversion to composites or hybrid systems. Photo Credit: Stellantis. Aluminum matrix composites (AMCs), known for their lightweight, high strength, and excellent corrosion resistance, have demonstrated substantial potential in vehicle aesthetics, interior trim, power systems, and components manufacturing. The presented work focuses on optimizing a heavy-duty TATA 1612 truck chassis (ladder type frame) by substituting its material from conventional steel with potential metal matrix composite.
Heterogeneity design is a promising strategy to solve the strength-ductility/toughness tradeoff in metal matrix composites (MMCs) via maximizing the intrinsic and extrinsic toughening mechanisms. In this review, we first defined metal matrix composites with structural heterogeneity as heterostructured metal matrix composites (HSMMCs). Automotive chassis is used for supporting the functioning structure and balancing on the road. Being an initial requirement chassis vehicles like trucks, trailers, and semi-trailers have stepping skeleton (ladder chassis).The current chassis mass with traditional material is 1560 Kg which is made up of structural steel, whereas the chassis mass with Aluminium carbide metal matrix composite material is 523.45 Kg.Abstract: With increase in fuel prices and demand for lightweight materials in manufacturing of Heavy Motor Vehicle (HMV) chassis is high, the current research envisaged the application of metal matric composites (MMC’s) in the manufacturing of chassis structures.
For this we have taken three materials like structural steel, carbon fiber and Aluminium silicon carbide metal matrix composite. The automotive chassis is the vehicle's base, providing.
Results shows that, the mass of chassis is 62.564Kg and 71.502 Kg using Graphite Al GA 7-230 and Al6092/SiC/17.5p MMC respectively whereas the actual mass is 214 Kg in case of conventionally used Structural steel alloy. Therefore, a significant amount of mass is reduced considering a number of other performance factors. 1. Introduction.
Metal-matrix composites offer considerable promise to help automotive engineers meet the challenges of current and future demands for recyclable, fuel-efficient, safe, and low-emission vehicles. These materials can be engineered to match the design requirements of automotive power-train or chassis components. Composite and hybrid components reduce mass, increase functionality on electric and conventional passenger vehicles. As automakers seek to reduce the curb weight of conventional and electric vehicles (EVs), metal chassis components have become a significant target for conversion to composites or hybrid systems. Photo Credit: Stellantis.
box electric company
Aluminum matrix composites (AMCs), known for their lightweight, high strength, and excellent corrosion resistance, have demonstrated substantial potential in vehicle aesthetics, interior trim, power systems, and components manufacturing. The presented work focuses on optimizing a heavy-duty TATA 1612 truck chassis (ladder type frame) by substituting its material from conventional steel with potential metal matrix composite. Heterogeneity design is a promising strategy to solve the strength-ductility/toughness tradeoff in metal matrix composites (MMCs) via maximizing the intrinsic and extrinsic toughening mechanisms. In this review, we first defined metal matrix composites with structural heterogeneity as heterostructured metal matrix composites (HSMMCs).
box electric fan manufacturers
Automotive chassis is used for supporting the functioning structure and balancing on the road. Being an initial requirement chassis vehicles like trucks, trailers, and semi-trailers have stepping skeleton (ladder chassis).The current chassis mass with traditional material is 1560 Kg which is made up of structural steel, whereas the chassis mass with Aluminium carbide metal matrix composite material is 523.45 Kg.Abstract: With increase in fuel prices and demand for lightweight materials in manufacturing of Heavy Motor Vehicle (HMV) chassis is high, the current research envisaged the application of metal matric composites (MMC’s) in the manufacturing of chassis structures.
Weight Optimization of Chassis of an Automotive
Structural analysis and weight optimization of automotive chassis
$362.99
chassis metal matrix composites|Structural analysis and weight optimization of