sheet metal bend relief formula Bend allowance formulas: For bends between 0 and 90 degrees, the formula is as follows: ß – bending angle (°) For bends between 90 and 165 degrees the formula is: For bends over 165°, there is no need to calculate .
Karl from Make It Kustom makes the ‘Mother Tucker’ — a heavy-hitting DIY nylon-tipped hammer that is perfect for shrinking sheet metal quickly when used with a sand or shot beater bag or shrinking stump.
0 · solidworks sheet metal relief cut
1 · solidworks sheet metal corner relief
2 · solidworks sheet metal bend relief
3 · sheet metal fabrication design guide
4 · sheet metal corner relief chart
5 · sheet metal bending chart
6 · sheet metal bend relief guidelines
7 · auto relief solidworks sheet metal
50400 - Super 50, 8-Port, 8 Terminal, Grey/Black Plastic, Surface Mount, .
Bend Relief - When a bend is made close to an edge the material may tear unless bend relief is given. Figure "A" shows a torn part. Figure "B" shows a part with the edge a sufficient distance .
With a 90-degree bend, the equation for your bend relief should be: Material Thickness + Bend Radius = Bend Relief, or, 0.10 in (2.54mm) + 0.030 in. (0.762mm) = 0.13 in. (3.302mm). This tiny adjustment to your CAD . Learn how to accurately calculate bend allowance with our easy-to-understand formula. Improve your sheet metal bending operations and achieve precise results every time.
Sheet Metal Bending Calculation. Bend Allowance (BA) BA = [ (0.017453 × Inside radius) + (0.0078 × Material thickness)] × Bend angle, which is always complementary. The length of the neutral axis is calculated as a bend . The article discusses making small holes and when to use a punch or laser cutter, inside radius measurements and how they differ depending on whether you are coining or air bending on a press brake, and adding bend .
Bend allowance formulas: For bends between 0 and 90 degrees, the formula is as follows: ß – bending angle (°) For bends between 90 and 165 degrees the formula is: For bends over 165°, there is no need to calculate . SHEET METAL Training with TOBY: www.TooTallToby.com/training More SOLIDWORKS SHEET METAL videos: https://youtube.com/playlist?list=PLzMIhOgu1Y5deswXMjjl9J.Bend relief is provided at the end of the bending edge in sheet metal design to avoid any crack tearing in the corner. Recommended Bend Relief height is always more than two times of sheet thickness plus bend radius.Mastering bend calculations in Onshape is a powerful skill that enhances the accuracy and efficiency of your sheet metal designs. By understanding the nuances of bend allowance, K Factor, and bend deduction as well as .
To eliminate this, a bend relief is added so the edge of the sheet metal is perpendicular to the bend. In general, a minimum bend relief is equal to the material thickness plus the inside bend radius. If it is OK for the metal to .
Bend Relief. Synchronous sheet metal is pretty cool, even cooler than just normal synchronous modeling, if you’ll excuse that word. For example, if you make a partial flange as above using all the defaults, the software makes . Sheet metal bending can be done using many methods. We discuss those along with springback, bend allowances, k factor, design tips etc. . constant; ir – inside radius (mm); t – sheet thickness (mm) Bend allowance . Factors Influencing the Minimum Bend Radius. The minimum bend radius of the sheet metal is affected by several factors, each of which is of specific importance in determining the most desirable degree of bend that would prevent collapse or paper deformation. tAng factors include:. Material Type: Different materials have varying levels of ductility and tensile strength, .
A feature bend is different from an individual bend, in that the feature bend is an actual sheet metal feature. For example, when you have a Sketched Bend in the FeatureManager design tree, the Sketched Bend feature is the sheet metal feature, and SketchBend is the individual bend that is absorbed in the Sketched Bend feature.
For this example, using 0.119” Mild Steel and bending at 90°, we will have a bend deduction value of 0.194” for each bend which is where we get the total length of 17.612.The options available to customize sheet metal Bends. Sheet Metal . Bend relief. Bend notch. Bend cut out. . Formula Curve. Projection Curve. Iso-Parametric Curve. Projection Combine Curve. Wrap Curve. Bridge Curve. 3D Curve. Trim/Split 3D Curves. Merge Curves. 3D Curve Edit.Step-1: Calculate the value bend allowance for the required sheet metal bend by using the below formula. Bend Allowance (BA) = (Π/180) × ( R + K×T) × A. Step-2: Calculate the value of bend deduction from the values of bend allowance and outside setback.Bending is a fundamental process in sheet metal working that involves deforming a metal workpiece into a desired shape by applying force between two tools by a press brake: an upper tool (known as a punch) and a bottom tool (known as a V-die). Bending can improve a part’s structural integrity by increasing part stiffness, redistributing stress within a part, and help .
When you specify bend relief, it is applied to the source face from which the flange is constructed. For example, when constructing a partial flange that is centered on the selected edge (A), bend relief is added to the source face (B) on both sides of the flange. . Sheet Metal Bend Formulas. Constructing flanges. Adding sheet metal .Bending diagram Image credit: https://www.custompartnet.com Bending Direction. Sheet metal displays anisotropic behavior when being bent, and direction matters to prevent general manufacturing defects like cracks and tears during the bending process. If sheet metal is bent in line with the direction of the metal fibers, the likelihood of experiencing a crack or tear at the . Bend radius is the smallest possible inner curvature that can be achieved when bending sheet metal without causing damage. For sheet metal up to 0.125" (⅛") thick, the industry standard bend radius is 0.030". Designing with this standard can reduce lead time and costs. If you have thicker materials or specific requirements, ASM can provide .
safco locking steel suggestion box black 4232bl
A Bend Relief avoids the sheet metal tearing if the bend is made at the edge of the material. . Bend height is calculated using the following formula, Bend Height (H) = 2 x Sheet Metal Thickness (t) + Bend Radius (ir) To avoid the distortion of the bend, it is must to keep the bending height greater than twice the thickness of the sheet metal . With this bend allowance calculator, you will learn how to calculate the length of a sheet metal bend so you can optimally create metal bendings without a bend allowance chart. It works as a bend deduction calculator too! This tool calculates bend allowance/deduction based on material thickness, bend angle, inside radius, and k-factor, as you will learn from the bend .minimum bend radius because most sheet-metal manuals, including AC 43.13-1B, have a minimum bend radius chart available for quick reference. (Figure: 2) The tool, which we use for bending sheet-metal, is called a “brake”. A sheet-met-al brake used for aircraft aluminum has either fixed or interchangeable jaws with aUsually I like to have the minimum bend radius as my thickness and the bend length is determined by a formula (you can look this up on google). . The sheet metal thickness is 0.08", bend radius is 0.05". . measured from the outside of .
The bending deduction in Solidworks is only used for the calculation of 90-degree bends in sheet metal. However, it can also be used for the calculation of non-90-degree sheet metal unfolding, but the bending . Manually calculate the K-Factor using the measure of sample sheet metal parts that were bent using the following formula: Note: Bend allowance is part between initial flat patter length of desired edges (arc length of the neutral axis through the bend): 6.0mm copper sheet bending allowance: 10.3; 8.0mm copper sheet bending allowance: 12.5; 10.0mm copper sheet bending allowance: 15; 12.0mm copper sheet bending allowance: 17; 3.0mm stainless steel with V25 allowance: 6; 3.0mm stainless steel with V20 allowance: 5.5; For copper plates thicker than 6.0, the allowance for the lower die is V40
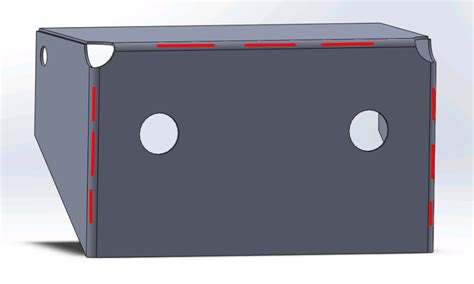
Sometimes this notch is used for parts with a large bend radius. The previous notches can be used with a large bend radius if a relief hole or slot is used in the corner (see Bend Reliefs). If no relief distance is called out on the print and you are using a large bend radius with this type of notch then to be safe use a minimum distance of the .When sheet metal is bend, the inside surface . the metal thickness (0.445 * T) ! Formula charts are available for calculating bend allowance Prem Mahendranathan . BEND ALLOWANCE Cont ..4 Prem Mahendranathan . . RELIEF HOLE ! Wherever two bends intersect, material must beBend relief. Bend notch. Bend cut out. . Formula Curve. Projection Curve. Iso-Parametric Curve. Projection Combine Curve. Wrap Curve. Bridge Curve. 3D Curve. Trim/Split 3D Curves. . Convert to Sheet Metal för att bocka plåt från importerad geometri. Övning 65 | Importinställningar.
To enhance the readers’ understanding of basic concepts in sheet metal design calculation, the following points will be summarized and explained:. The definitions of the two bending algorithms: bend allowance and bend deduction, and their connection to the actual sheet metal geometry. The relationship between bend deduction and bend allowance, and how .BEND ALLOWANCE: Sheet metal stretches minutely as it is being formed. The greater the inside bend radius is the less the stretching. Also material hardness or elasticity has a lot to do with how much it stretches. . EMPIRICAL FORMULA: Bend allowance = (.0078 x MT + .017453 x BR) . We use the Bend Deduction formula every day at Approved Sheet Metal to compute our standard sheet metal bend gains chart. This chart serves as a handy reference for bend deductions with a variety of materials and thicknesses, and is a valuable resource for understanding how sheet metal stretches when bent. Why Bend Deduction is ImportantStudy with Quizlet and memorize flashcards containing terms like Bend Radius, Measuring the size of the bend, the diameter is and more. . Aircraft Sheet Metal (Bending) Flashcards; Learn; Test; Match; Q-Chat; Get a hint. Bend Radius. Is considered to be the curvature of the bend. (Measured at the inside curved surface of the bend.) 1 / 44. 1 .
A feature bend is different from an individual bend, in that the feature bend is an actual sheet metal feature. For example, when you have a Sketched Bend in the FeatureManager design tree, the Sketched Bend feature is the sheet metal feature, and SketchBend is the individual bend that is absorbed in the Sketched Bend feature.
solidworks sheet metal relief cut

Precision sheet metal fabrication is a common manufacturing process where the structure of a metal workpiece is cut, bent, and assembled by machining. There are any number of operations that are performed in the creation of a finished sheet metal product.
sheet metal bend relief formula|sheet metal corner relief chart