tig welding corners sheet metal TIG (Tungsten Inert Gas) welding excels at joining thin sheet metal. It provides superior control, minimal distortion, and clean, strong welds. By using a non-consumable tungsten electrode and inert gas shielding, TIG allows for precise .
How to wire an electrical junction box. A junction box is used to add a spur or to extend circuits and direct power to lights and additional sockets. Advice on wiring electrical junction box with .
0 · welding thin to thick metal
1 · welding stainless steel sheet metal
2 · welding sheet metal without warping
3 · welding 14 gauge sheet metal
4 · tig welding stainless sheet metal
5 · tig welding automotive sheet metal
6 · mig welding galvanized sheet metal
7 · 18 gauge weldable sheet metal
Right Angle Bracket for Wood Pole Mounting.
In this video we go through the process of welding, grinding, and polishing an outside corner weld. We are tig welding the stainless steel sheet metal then using appropriate abrasives to. CORNERS AND WELDING. Proper technique on corners that need to be welded is necessary to reduce cost and increase the overall .
Preventing burn-through and warping when welding sheet metal is all about controlling the heat. Choose the right welding process and filler metal, and follow these . Tig Welding “Outside Corner Joints” in sheet metal is a great way to frame up a water tank, battery box, tig cooler, tool tote tray, or just a cool box to hold soapstone and .
Here are some tips, settings, and arc shots to help your chances of making a good weld on an outside corner joint. I used a #8 furick clear cup on some of these welds to help with the filming.TIG (Tungsten Inert Gas) welding excels at joining thin sheet metal. It provides superior control, minimal distortion, and clean, strong welds. By using a non-consumable tungsten electrode and inert gas shielding, TIG allows for precise . Did you know that TIG welding is the best option for sheet metal? The biggest problem any welder is going to face when it comes to sheet metal is the heat in. TIG Welding thin stainless steel sheets or tube is a challenging task that requires very high welder skills- both manual as well as equipment setup.
Video shows Tig Welding Edge Welds with detailed arc shots - Aluminum, Stainless, Carbon Steel from .125" (3.2mm) down to .050" (1.2mm) thickness.
Ensure snug fit-up for butt, lap, T, corner, and edge joints. An accurate fit-up contributes to both the aesthetic and structural integrity of the weld. Following these expert tips with precision and care, you can improve your .
In addition, they require a large amount of weld metal. Types of Corner Joint. There are many different types of corner joints that can be used when joining two pieces of wood together. The most common type of joints are: . For thin sheet metal, use autogenous tig welding to .Another joint type in sheet metal work is the flush corner joint. A flush corner joint is only used on lighter sheet metal (12 gauge or lower). . The difficulty in welding sheet metal is that you need to get good penetration to make a nice weld and . Utilize filler metals (wires) that are slimmer as compared to reedy sheet metal. Numerous welders utilize 0.023-inch diameter wires and 0.024 inches for slimmer sheet metals. 18-gauge metals such as stainless steel have . In this video we go through the process of welding, grinding, and polishing an outside corner weld. We are tig welding the stainless steel sheet metal then .
For thin sheet metal welding it can be 30 ampere while for thicker (e.g. 1/8” square groove weld)- it can go up to 220 ampere for example. GMAW-S gives low heat and makes it easy to use in all positions on sheet metal, low carbon steel, low alloy steel, and stainless steel . Look at the TIG welding amperage charts below for information to help you with any weld, no matter the material, size, or anticipated outcome. TIG Welding Chart Based on Material and Shielding Gas. The amperage required when TIG welding is highly affected by the type of metal you are working with and how thick that metal is.Mastering TIG Welding Techniques for Sheet Metal. TIG welding sheet metal demands precision and skill. Let’s explore the techniques that will elevate your welding game. Key Principles of TIG Welding Sheet Metal. Success in TIG welding sheet metal hinges on several core principles: Maintain a short arc length, typically 1/8 inch or less. Welding Processes for Thin or Sheet Metal. Each welding process requires specific precautions and equipment setup for a successful sheet metal weld. So, let’s discuss the preparation needed for each arc welding process before proceeding to the common problems with thin gauge welds. MIG Welding (GMAW) MIG welding works fine for thin materials .
In this video I show how to set up and tig weld thin metal. There are a lot of different steps to take and I try to make it as easy as possible. From how to . Most of these machines will need sheet metal enclosures, most likely made out of 16 gauge mild or stainless steel sheet. I'll likely be having these parts all laser cut and then I'll weld them up in my shop, so I'll be running beads along the corners of a lot of boxes basically.Did you know that TIG welding is the best option for sheet metal? The biggest problem any welder is going to face when it comes to sheet metal is the heat in.

TIG welding and tungsten metal work so well when welding mild steel because the Tungsten keeps the arc with a consistent temperature of 11,000 degrees F. Tungsten brings us a high melting point, and also offers excellent electrical conductivity as you weld, so the tungsten electrode won’t ever burn up. . we focus on the side of the heat .Tig Welding Video shows arc shots of a Stainless Steel Weld Repair In addition to pulse tig settings, chill blocks and bars are very necessary in order to limit distortion on thin sheet metal. Pulse Tig settings for thin outside corners It is always important to choose the right type of joint for your project. Strength is necessary on thick joints. A fully open corner has the potential to produce the strongest type of corner weld. With thinner pieces, like sheet metal, flush corners will do the job adequately. With intervening thicknesses, a half-open corner weld may be best.
I was not paying attention to the thickness of sheet you were specifying .9 of a mm is equivalent to 20gauge sheet metal. In normal industrial practice it is more common to put a spot welded tab flange with a sealant, rather than a weld. If you insist on torch welding this part (TIG) heliarc is recommended.Precision Machine Fabrication is your trusted sheet metal expert in Winston-Salem, NC. Get started on your custom project today! 919-231-8648 [email protected] Request a Quote
welding thin to thick metal
welding stainless steel sheet metal
While running on clean metal a lower balance will spread out your puddle allowing for a greater amount of build-up, while at the same time not penetrating as deep into the base metal. As you can probably imagine this isnt ideal, and is even worse when it comes to aluminum as its already difficult to get proper penetration when learning.
TIG welding sheet metal. Forget the larger 1/8-inch tungsten electrode and use a smaller one. Ceriated tungsten are preferred, with thoriated tungsten as a second option. The diameters down to .020, .040 and 1/16-inch tungsten are popular. Smaller electrodes start easier and perform better at lower heat settings, which helps prevent burn . 3. Adjust Your Torch Angle. Changing the torch angle when MIG welding goes a long way to preventing burn-throughs. Make sure you adjust the angle to shorten the distance between the tip and the metal, no matter the welding position you work in.This will make the arc more stable, giving you more control over the weld and lessening the chance of burn-through.

welding sheet metal without warping
The corner welding joint is similar to tee-joints, except that in this, one of the parts is fitted at the corner of the second part (hence the name, corner joint). Types Of Corner Joints. In welding, the commonly used corner joints are of following types: Fillet weld corner joint, Flush or closed corner joint, Half-open corner joint, and
welding 14 gauge sheet metal
On this episode of Make It Kustom, I continue to repair the rust on the GMC G10 boogie van. We talk in depth about technique for repairing rust and welding o. Why You Should Spot Weld With a TIG Welder. Though the processes of spot welding and TIG welding seem drastically different, they share enough commonalities that a TIG welder can indeed be used to produce spot welds. Namely, both processes use an electric arc instead of an open flame to melt metal to create a join.An oustide corner joint is one of the easier joints to weld and very often, in sheet metal thickness, does not even need filler rod. But for the sake of instruction and a better how to tig weld steel video, I used filler rod except for one small clip. TIG Welding Sheet Metal. Tungsten Inert Gas (TIG) welding, or Gas Tungsten Arc Welding (GTAW), requires more manual dexterity, offering high levels of precision and control. . Ensure snug fit-up for butt, lap, T, corner, and edge joints. An accurate fit-up contributes to both the aesthetic and structural integrity of the weld.
Table of Contents. 1 Spot Weld vs. Seam Weld; 2 7 Things to Know About Spot Welding ; 3 Sheet Metal Part Design for Manufacturing Tip. 3.1 CORNERS AND WELDING; 4 Spot Welding FAQ. 4.0.1 What is the difference between spot welding and seam welding, and when should I choose one over the other?; 4.0.2 What is plug welding, and when should I .
tig welding stainless sheet metal
I would spend some more time working on ataugenous welding. Just take a piece of sheet metal and scribe out a bunch of 1" squares and center punch the corners. Then run your puddle along the lines making sure to fully close up the punch marks without melting through. Once you can do that reliably you can start working with filler. In general, though, TIG welding sheet metal can be done like TIG welding any other metal. Get your amps going, stick to a consistent travel speed and dab, dab, dab. If the fit-up is tight (and thin) enough, you don’t even need filler, but you should keep it on hand to add if needed. For example, if the weld was opening up and widening, you .
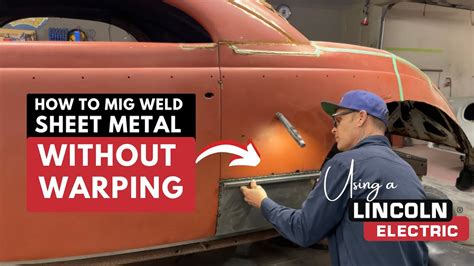
Metal framing doors are an essential component of any building project, providing strength and stability to the overall structure. Whether you’re constructing a commercial building or renovating your home, proper installation of metal stud doors is crucial.
tig welding corners sheet metal|welding sheet metal without warping