how to mig weld rusted sheet metal On this episode of make a custom I pull the 81 G10 Van in for a rust repair patch step-by-step mig welding. Check out how to make your own tucking fork here: • How To Make a Tucking Fork to. We specialize in quick deliveries for custom designed enclosures and metal fabrications to meet your specifications for indoor, outdoor and vandal-resistant conditions. All of our products meet or exceed UL, NEMA, NEC Standards.
0 · welding sheet metal without warping
1 · welding 24 gauge sheet metal
2 · welding 22 gauge sheet metal
3 · welding 16 gauge sheet metal
4 · welding 14 gauge sheet metal
5 · mig welding thin sheet metal
6 · mig welding sheet metal basics
7 · mig welding automotive sheet metal
Sigma's weatherproof closure plugs help keep moisture from the electrical wiring by closing unused holes in weatherproof boxes, extension rings or covers. In a world that runs largely on electricity, junction boxes are crucial to protecting .
In this video I demonstrate how to set up your mig welder so you can weld thin sheet metal. We also showed in this video how to make your pattern, fit and weld it in. I demonstrated.
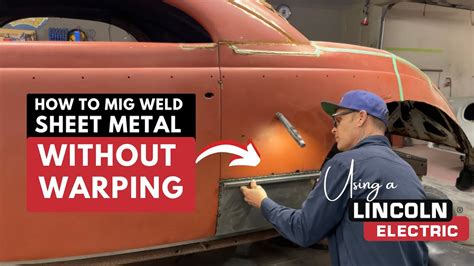
On this episode of make a custom I pull the 81 G10 Van in for a rust repair patch step-by-step mig welding. Check out how to make your own tucking fork here: • How To Make a Tucking Fork to.
We are going to show you how to weld sheet metal that is rusted out and in bad shape. This is very common in the welding restoration of old cars and tractors. Today's weld project.
Use a wire brush or grinder to clean the metal. Clean metal leads to better welds. Wipe the surface with acetone or a similar solvent. This removes any remaining contaminants. .
Stick welding with 6010 and 6011 rods on pure rusted metal is the best option without any surface cleaning. If you can grind and clean the surface the MIG welder will do a much better job and give a more aesthetically .
The problem with welding sheet metal or thin gauge steel is that you can easily blow holes in the panel and create a big mess quickly. We decided to give you some tips when . Master the Art of Rust Repair on Sheet Metal with Luke Merrill. Discover expert insights on repairing rust corrosion through fabrication and welding techniques. Learn step-by-step instructions to restore your metal . Still, it’s possible to weld thin sheet metal using the MIG (GMAW), TIG (GTAW), and stick (SMAW) processes. But MIG and TIG provide the best results. This article will teach you how to weld thin gauge metal using each arc . Preventing burn-through and warping when welding sheet metal is all about controlling the heat. Choose the right welding process and filler metal, and follow these common tips to help ensure success.
In this Video JD goes over why you should always keep a pack of copper backers in your welding cart! MORE INFO: https://www.eastwood.com/welders-helper-3x3-s. On this episode of Make It Kustom, I'm back on the Model A Roadster welding on the hood and shaving the cowl using both MIG welding and TIG welding technique. In the rest of this article, I’m going to share my process and tips for welding rusty metal to help give you the best outcome. 7 Steps to Weld Rusted Metal. Now that you know that you can weld rusty metal, the next question is .
Here's some tips if you're having trouble mig welding thin sheet metal. Check out my custom mini parts available:Urchfab Front Subframe Kit: https://www.ebay. Importance of welding car sheet metal. Body panels come loose, rust and eventually need to be replaced. This can be very expensive and inconvenient. . This is why gas-shielded welding is also known as shielded metal arc welding, or SMAW. Gas-Shielded MIG Welders also function in SMAW fashion, but they use a gas blend of Argon and CO2 instead . Try supporting your metal from the backside with something. Having something like a table underneath or even a little copper backer will help support that molten weld pool and it will act like a little bit of a heat sink. You want to avoid welding sheet metal that’s floating in . Sheet metal MIG Welding 101Episode 85 Manic MechanicRobert McCartney from McCartney Paint and Custom came in to give welding tips for those using a MIG welde.
If it is thin enough to have holes, the metal may be hard to mig weld. I fill trim holes in good metal by holding a copper bar on the backside. I have painted over lead with no problems. JB Weld may be the way to go. Usually rust is much worse then what the outside surface is showing.
2828 ackley ave richmond colonial sheet metal
This all depends on the level of quality of the final product you want. For most rust repair jobs, MIG welding is just fine and more straightforward for a novice metal worker. Oxy acetylene would be my third choice, and arc welding would be my fourth choice. As with welding on any metal, shrinkage and warping will happen.
In today's episode of how to learn flux core welding for beginners, I cut up some pieces of scrap steel to show you guys the drawbacks of welding on rusty di.Master wire feed welding for sheet metal: Discover the best techniques and tips for creating strong, clean, and durable welds. . Is it necessary to clean the metal before welding? A: Yes, removing any rust, paint, or oil from the metal surfaces is crucial for a strong and clean weld. . Understanding the difference between MIG and TIG .
welding sheet metal without warping
In this video I will show you how to repair a rust hole on your car in a tight spot by mig welding a sheet metal patch in, knocking that patch down below the. Never go for a thinner base metal for auto body sheet welding to get the best result out of it. When starting to learn auto body sheet metal welding with a MIG welder, you should opt for a shielding gas that has a higher proportion of argon gas. It is better to use instead of a high percentage of CO2. Welding nearly always causes some distortion: the metal in and around the weld shrinks as it cools, and this shrinking often upsets the shape of the metal. Sheet metal is particularly sensitive to this type of distortion (often called warping) but there are ways to mitigate this characteristic, which we will detail here.
6. Prepare for Welding: Once your replacement panel is ready, you’ll need a welder. You can use flux core without gas, but it will make more sanding work. MIG welding with 75% Argon and 25% CO2 won't create much spatter and will create a much cleaner weld verses flux core. For a full guide on how to MIG weld with gas check out this video: MIG welding simplifies the feeding of filler metal, making the welder’s job easier. While the specific material may not be critical, the form of the filler metal is important when working with thin sheet metal. 3. Adjust the Torch . But remember, you have to be careful while welding thin sheet metal. It needs to have a balanced heat energy input. Otherwise, you will experience burn-through issues. How to Mig Weld Car Sheet Metal (Process) . In this video I show you how to set up your MIG welder and also prepare your metal for the plug welding process. I try to walk you through the entire process.
Up close and detailed, this video shows how to MIG weld patch panels into place for a rust repair that is easy to accomplish and long lasting. Tools and mat. Here's a few tips on repairing rust holes in car body panels.Wanna buy me a beer? https://www.paypal.com/donate/?hosted_button_id=WZS79GVX5VBJ2In . Mig welding sheet metal requires precision and control to prevent warping or burn-through. A thin wire and low heat settings are essential. . Before welding, the surface must be free of dirt, oil, and rust. Use a wire brush or grinder to clean the metal. Clean metal leads to better welds. Wipe the surface with acetone or a similar solvent .
Today we're going to demonstrate how to butt weld sheet metal using a Lincoln Electric mig welder. Like anything, there's a right way and a wrong way to butt. Remove any rust: Use a wire brush or sandpaper to scrape off any rust from the metal surface. If there is extensive rusting, consider replacing the damaged parts. Securely clamp or hold down the sheet: To prevent movement while welding, hold down or clamp securely onto a stable work surface. . Follow these 3 steps to understand MIG welding . Welding Processes for Thin or Sheet Metal. Each welding process requires specific precautions and equipment setup for a successful sheet metal weld. So, let’s discuss the preparation needed for each arc welding process before proceeding to the common problems with thin gauge welds. MIG Welding (GMAW) MIG welding works fine for thin materials .
For realist practise try welding some clean steel the same thickness sheet as you will use to make repirs. You will soon see how rust gives bad results when you start to weld rusty steel instead of the clean stuff you practiced with Good luck with the MMA on that! (can offer some pointers on welding thin sheet with a stick welder) Stick welding, or Shielded Metal Arc Welding (SMAW), is the best option for welding rusted metal. This is because stick welding uses flux-coated electrodes that burn through the rust. In addition, the welding rods for rusty metal contain de-oxidizers that help to neutralize contaminants in the weld. Here are the basic steps to welding rusty metal:Most of his work is sheet metal repair and fabrication. He uses basic tools most of the time. Occasionally, he needs to use a sheet metal brake or an English wheel, but he usually just uses a small body hammer, an angle grinder, and a 110V welder.
welding 24 gauge sheet metal
welding 22 gauge sheet metal
From smaller waterproof boxes for electronics to large weatherproof electrical enclosures, we offer a variety of styles, sizes, and materials to choose from. With a watertight gasket, sealed enclosures are guaranteed to keep electronic and electrical equipment safe in wet conditions.
how to mig weld rusted sheet metal|mig welding thin sheet metal